Technique
Quality that endures, quality that excites.
Anyone using a SUBAL housing can feel the passion and no-compromise commitment to quality we apply down to the smallest part. Our designers and production staff accept nothing but perfection in producing housings for each camera model. Only the best, top grade materials pass our tough “handmade“ quality control. Less obvious at first glance, are the many improved features we build into our housings, innovations that have grown over decades of field and manufacturing experience. We believe only housings designed and built hand-in-hand with the photographer deserve the “handmade“ label. SUBAL quality wins hands down every time!
Handmade with handling in mind
These five simple words sum up the outstanding operational ease and superiority of a SUBAL underwater camera housing. After all SUBAL goes to great lengths to develop and implement innovative solutions that achieve maximum user-friendliness. As a result access to the most used camera functions is made as easy and comfortable as possible. Applying the “hands-on” philosophy all the way to final quality assurance comes at great cost but to us is a point of honor!
“Handmade” is our advantage
Here at SUBAL we pride ourselves in beating the competition regularly in producing a custom housing for brand new camera models. Every single member of our staff contributes their passion, experience and enthusiasm to achieving this outcome. Our emotional engagement is a defining feature at SUBAL. Obviously the application of the latest CAD/CAM technology throughout the entire manufacturing process is equally important in retaining pole position and pushing the envelope.
"Handmade" is our guarantee
Our staff makes a personal pledge to quality in every step of the manufacturing process. It is a matter of individual responsibility to achieve an outcome of which the entire team can be proud!
"Handmade" is our reliability
Literally handmade experience gained over more than five decades of development and production has crystallized into guiding principles for our work, and for our customers, into the confidence that comes with supreme reliability. All are decisive advantages ensuring you to be in good hands with SUBAL.
Advantage: Materials
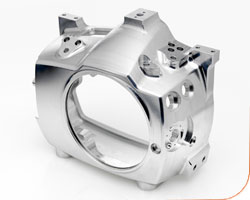
Because when it comes down to it, you want only the best materials! Therefore SUBAL housings are milled from a solid block of aluminum. This prevents unwanted air pockets and ensures absolute tightness. All housing parts and accessories are made of this same alloy, which is characterized by a high degree of seawater resistance. Additional heat treatment increases strength and hardness by about 30% and reduces the inevitable underwater deformations due to depth. Guaranteed are shafts, screws, and many other parts made of high-alloy nickel-chromium coated steel. Only high-quality engineering plastics are used – for the best durability and longevity.

Surface perfection through whole-part milling

Highly resistant to seawater
Advantage: Surface
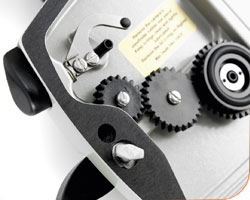
You want to have long-term fun with your SUBAL housing and we ensure that it is built for maximum durability: “hard-coating” produces wear and scratch resistance plus corrosion resistance in all aluminum parts to a superior level through a tough protective layer (up to 10 times that of an anodic coating). As additional wear-protection we add a high-quality, multi-layer powder coating.

Surface hardness and corrosion protection

Additional high-quality powder coating
Advantage: Frontports
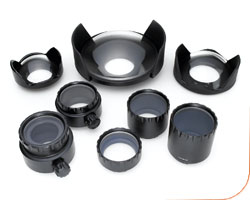
Front ports especially depend on hardness and dimensional stability. Therefore most SUBAL ports are made of polyacetal resin. With the larger dome ports a seawater-resistant light metal alloy is used and are then subject to the hard-coating process. The quality of your underwater photos depends on the material of the “windscreen”, which is why all SUBAL flat and dome lenses are made of perfect optical quality glass, which are also coated internally for optimum light transmission and better contrast performance.

Flat and dome panes made of optical glass

High-quality plastics for front ports
Advantage: Sealing
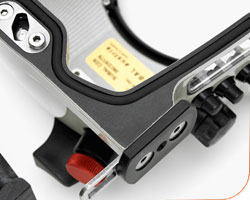
The primary role of an underwater housing is to maintain absolute watertightness! Therefore SUBAL only provide O-rings that have been proven in industrial use as well as in underwater technology: seawater resistant materials must also be resistant to all kinds of fats and oils. For extra thick housing and port o-rings an especially soft material is used with the advantage that small enclosed dirt particles are embedded! SUBALs innovative closure system can also exclude many problems resulting from careless handling. This keeps your housing reliably watertight for the long-term.

Special rubber compound for O-rings

Quick opening & closing thanks to the Quicklock closure system
Advantage: Usage
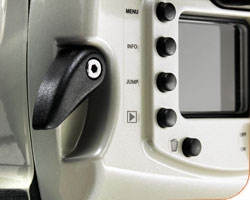
Which camera functions do you want to do without? We believe: none! Therefore, our housing offers by default a larger than average number of operations. This means the technical and creative possibilities of modern high-end SLR cameras are fully accessible to you, the underwater photographer. Wherever possible, the operating controls are optimized to be close to hand or in the camera position that you are used to – so avoiding having to re-think. The high-tech production, based on our 2ndSkin principle, results in the smallest possible dimension and weight – an advantage which should not be underestimated when it comes to handling and transport.

Precision thanks to state-of-the-art 5-axis CNS milling

Perfect accessibility of all controls

Quick opening & closing thanks to the Quicklock closure system
Advantage: LongLife
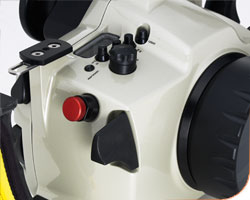
These items make a SUBAL housing more durable than you think! All plastic parts produced in spray technology are virtually identical, interchangeable and therefore fit as spare part even after many years. Then you can rely on all levers, knobs, gears, lens gear rings, caps etc. To ensure this, we pay with the choice of production methods on constant quality: Housing and injection molds are CNC machined in-house to guarantee the perfect matching from the first track to the last of a series. In addition, each individual case is controlled in all production steps by hand: Multiple print samples, adjustment of all operating elements, check the electronics, to name just a few examples.